Bosch 集团 Bosch Bamberg 工厂
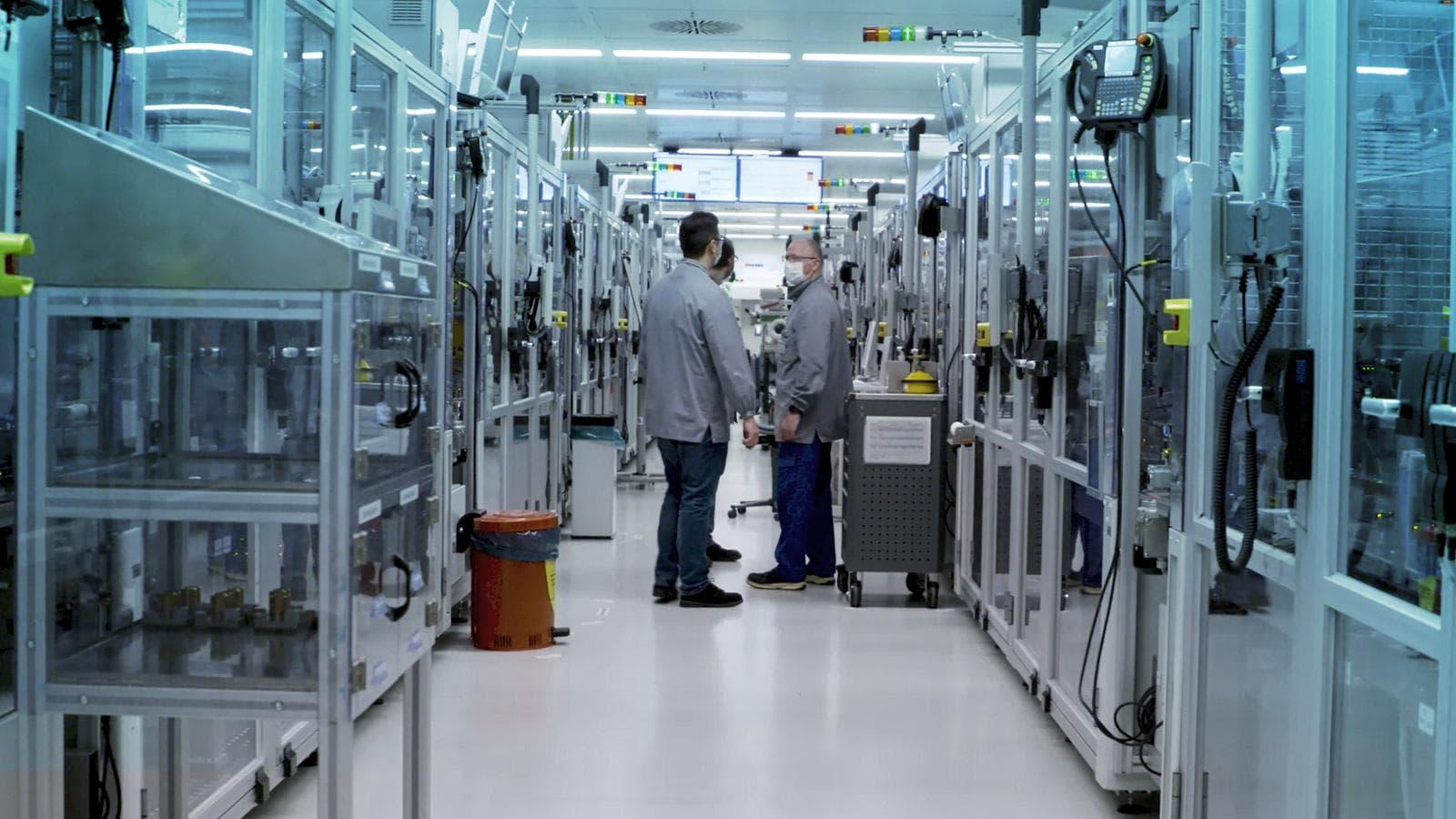
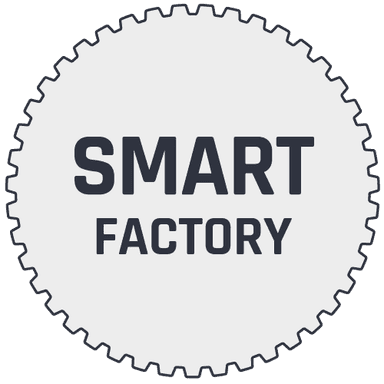
项目重点
博世班贝格不仅是博世集团在德国最大的制造基地,也是全球生产网络中柴油技术领先的工厂。 该公司正在投资扩大生产燃料电池和进一步开发内燃机部件。 作为工业 4.0 项目的一部分,汽油、燃气和柴油发动机喷油器的生产线将在四个地点实现完全自动化和数字化。
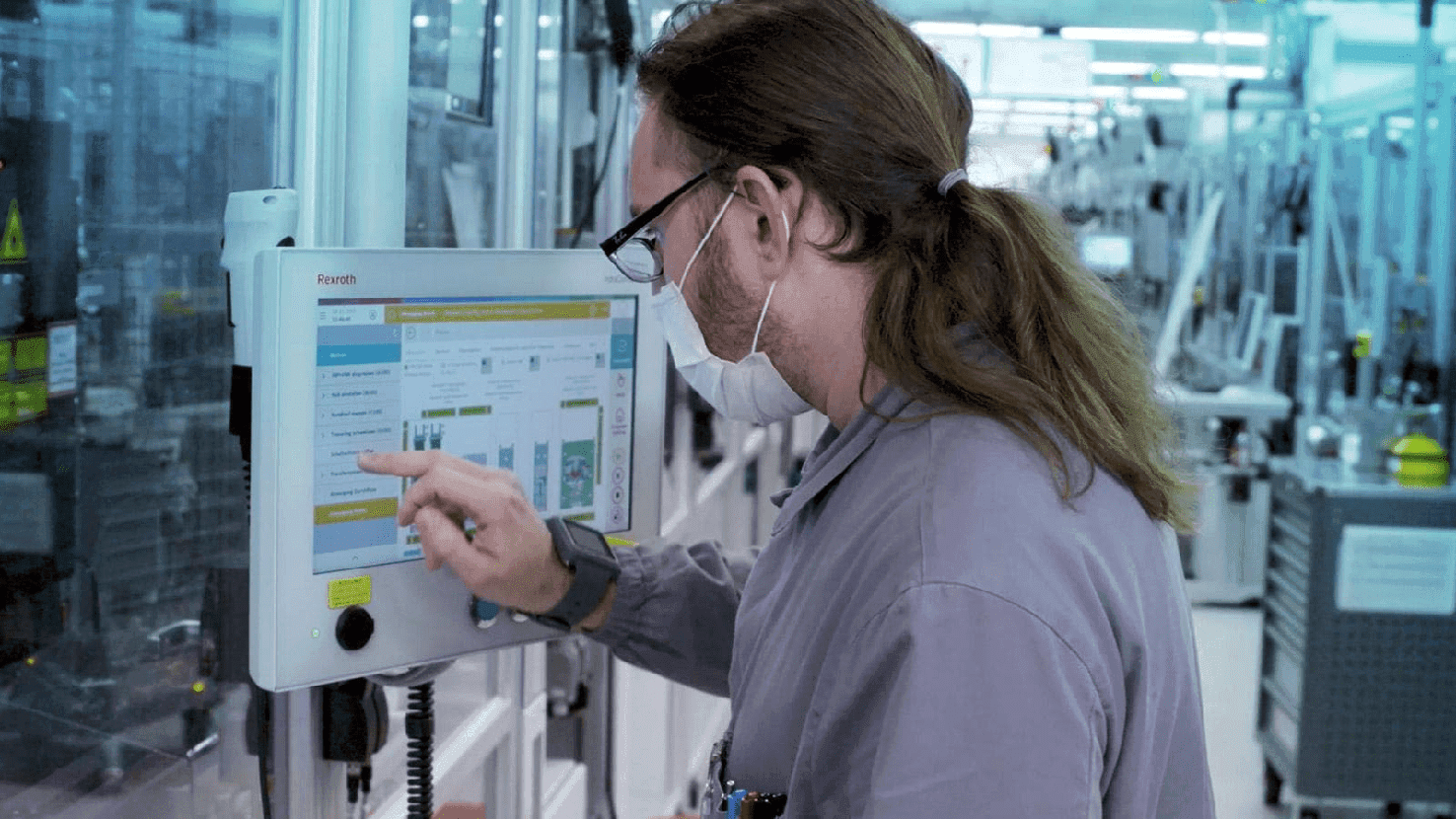
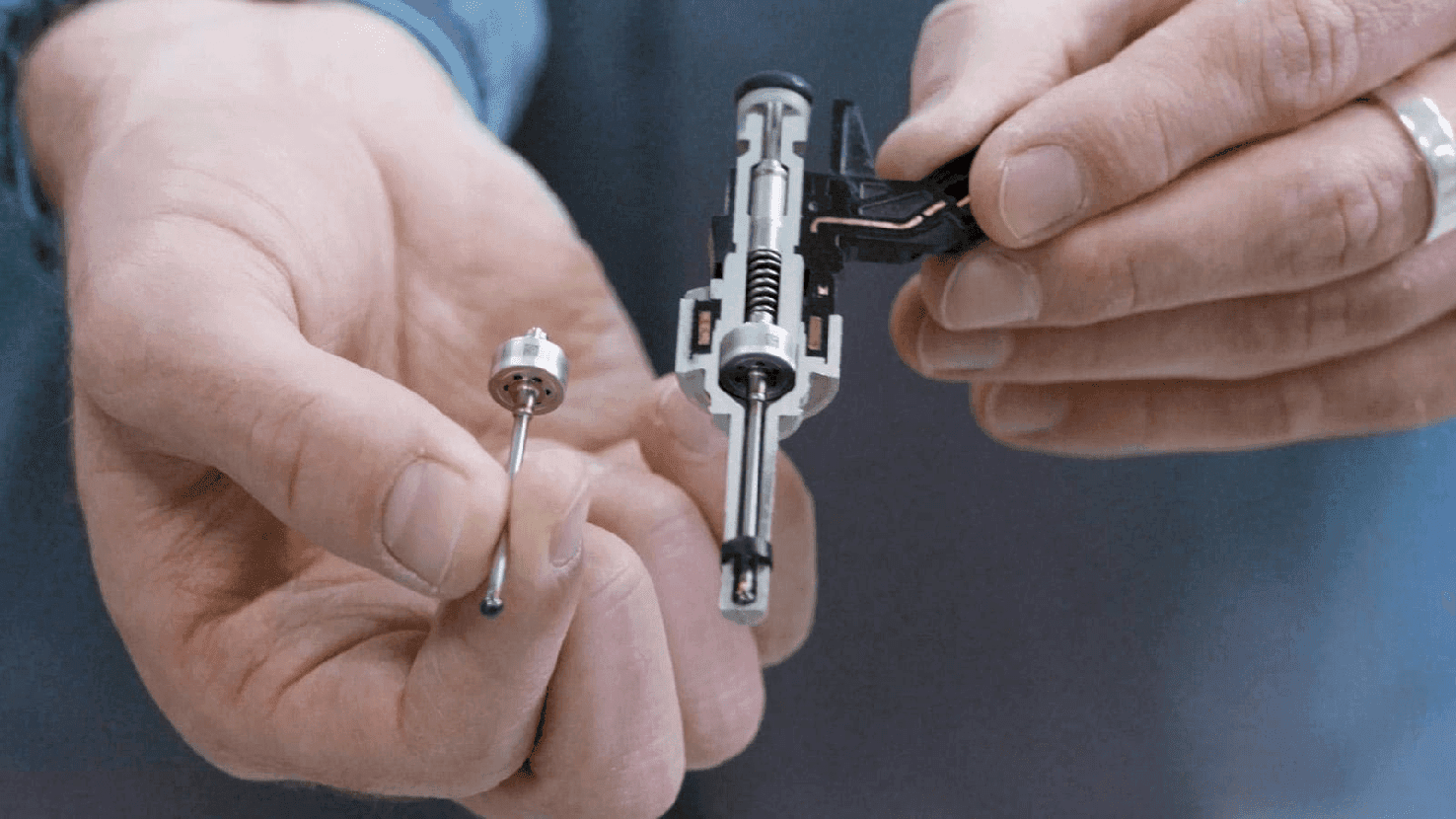
解决方案
第一条全自动生产线已经在班贝格建成。所有记录的数据都存储在可以通过 Web 界面访问的数据仓库中。未来,来自全球分布的各个生产线的流程和机器数据以及来自 ERP 的材料数据将在此处流式传输,以尽可能透明和精确地映射材料流的状态。
一个关键目标是简化向员工提供信息的过程。从收集的数据量中,应该可以快速且易于理解地获取信息,尽管自动化程度已经很高,但仍可实现进一步的改进,如无需联系 IT 部门的简单访问以及数据的可视化已经可以作为重要目标实现。
亮点:实现最佳连接的标准化
该公司使用 MES(制造执行系统)来控制、监控和自动化流程并记录生产数据。项目团队制定了机器集成的标准化要求——这使得以更有针对性的方式使用新技术并避免昂贵的系统改造成为可能。
此外,Borsch 将 MES 与 ERP(企业资源规划)连接起来,现在可以使用自动好/坏零件过帐和物料重新订购等功能,而且还能不断提高库存透明度和质量保证。
亮点:为预测准备信息
在新的生产线中,所有机器都与标准化的 IT 产品/平台连接:MES 收集过程和质量数据,数据仓库系统可以通过数据挖掘、可视化和 AI 支持从这些数据中获得新的见解,除其他事项外。偏差管理和异常检测引擎还允许在早期阶段检测到生产过程中的偏差并立即启动对策。
亮点:人机交流
智能手表会通知工人生产过程中的故障/异常情况。此外,该团队使用智能眼镜进行远程支持和其他目的,例如快速启动、更有效的维护或更轻松地将收集到的经验转移到工厂网络中。
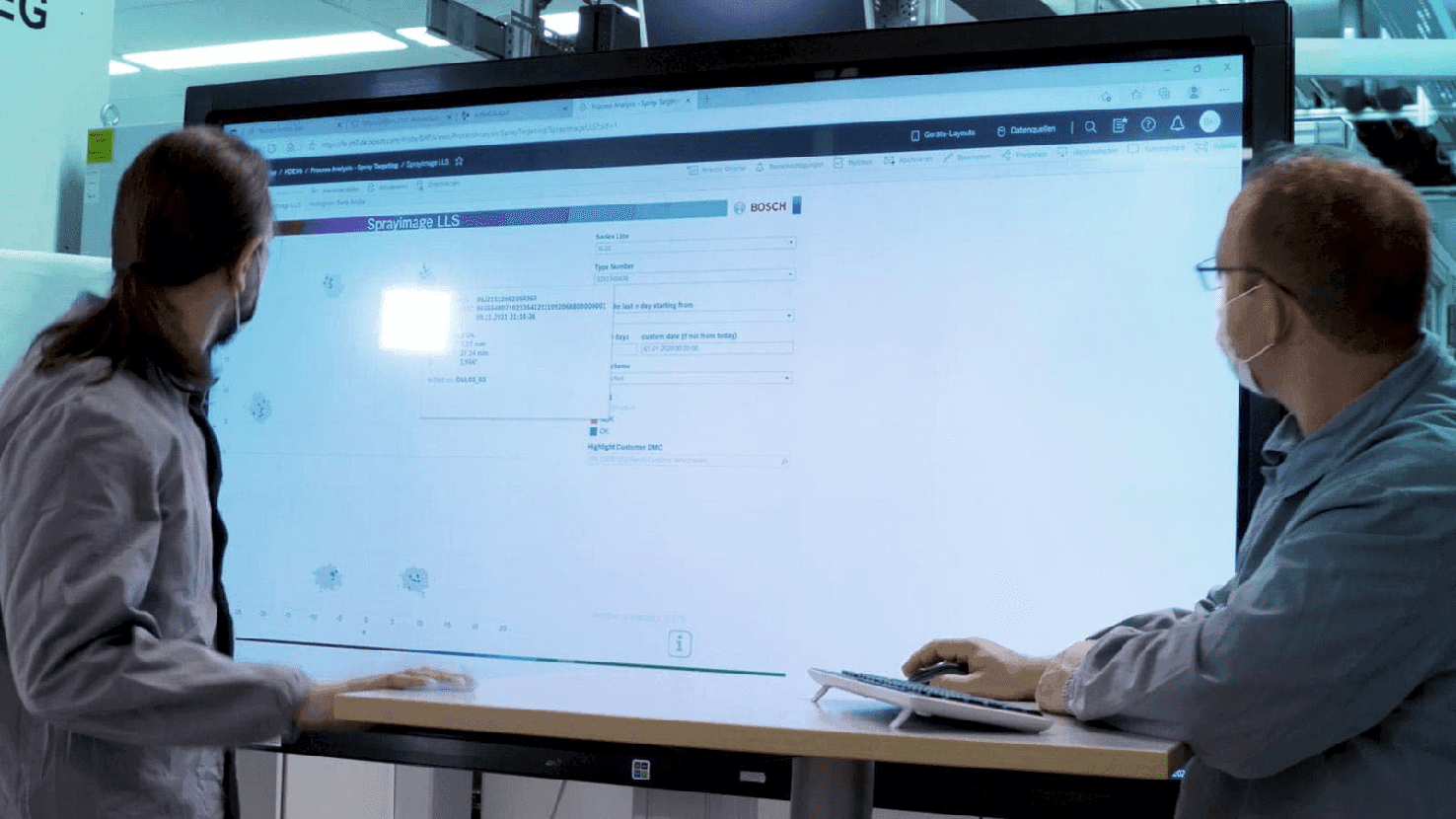
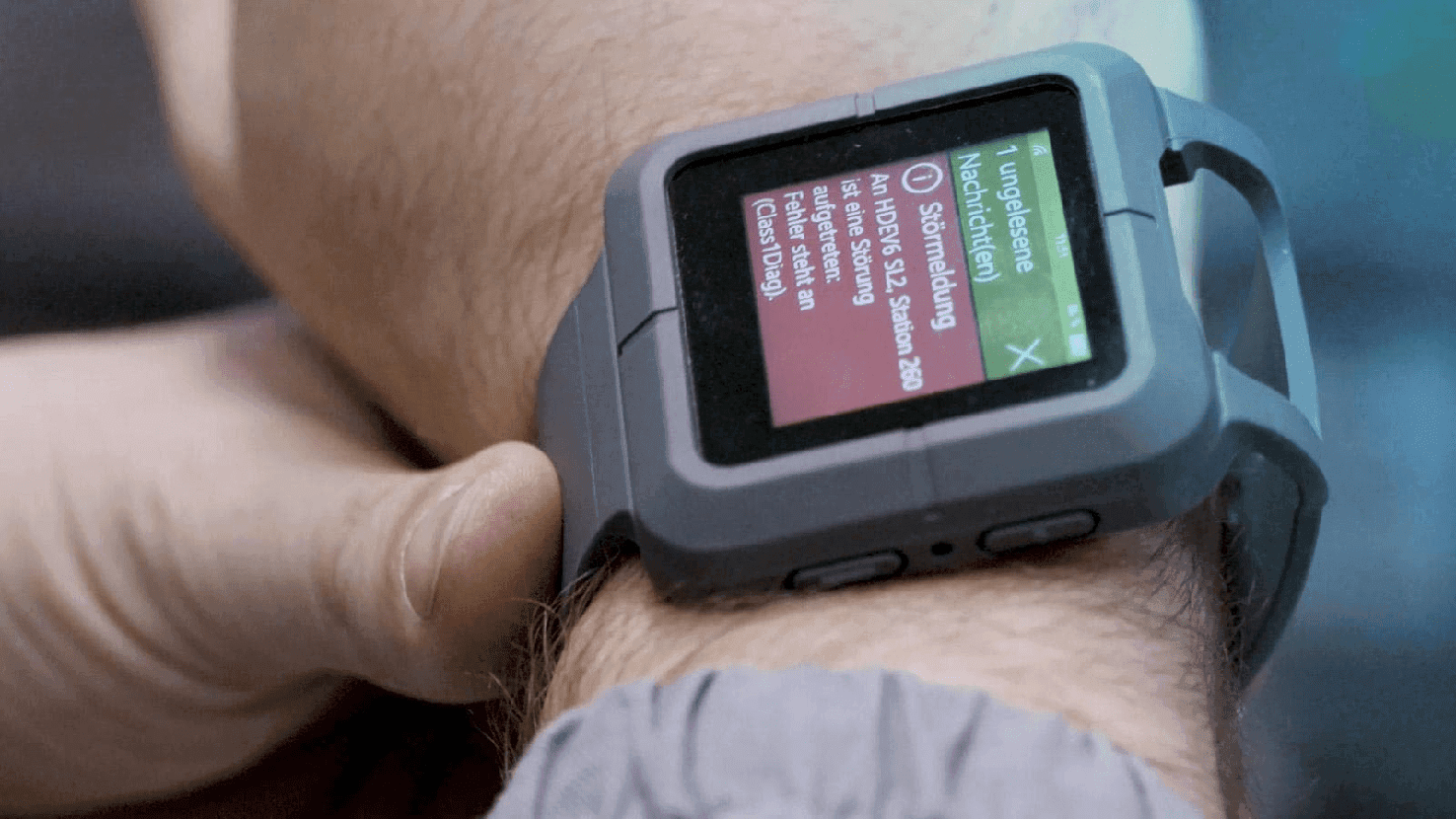
成果:
· OEE显着提高
· 缩短周期时间
· 在生产网络中节省两条完整的生产线
· 三年内平行引进多条全自动生产线
· 降低与生产直接相关的成本
· 客户的正向反馈
Bosch 集团 Bosch Bamberg 工厂